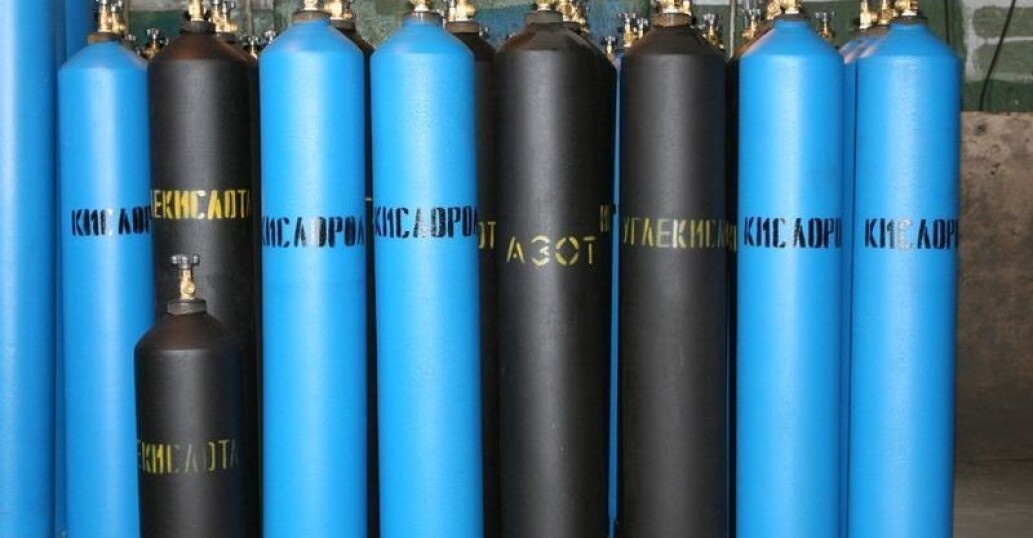
Расход газа на станке для лазерной резки
Лазерная резка — это довольно популярная технология. Высокая точность, эффективность и скорость делают ее популярной в различных отраслях, включая строительство, дизайн и т.д. Во многом лазерная резка зависит от использования специальных вспомогательных газов, которые используются в процессе. Правильно подобранный газ позволяет сократить время на выполнение работы, повысить ее эффективность, снизить затраты на рабочую силу.
Вспомогательные газы отвечают за удаление расплавленного металла, предотвращают окисление, а также влияют на скорость и качество резки. К таким обычно относят кислород и азот. Они отличаются друг от друга по характеристикам, что важно учитывать при принятии окончательного решения. Например, кислород лучше подходит для резки углеродной стали, тогда как азот предпочтителен для нержавеющей стали.
Правильная настройка параметров лазера и верно подобранный вспомогательный газ позволяют добиться эффективного результата, что значительно снижает затраты на последующую обработку.
Виды вспомогательных газов
К ним относят кислород и азот. Без них сегодня уже трудно представить себе лазерную резку.
Кислород
Это газ с высокой химической активностью. Он делает резку более быстрой и эффективной, а также помогает легче удалять расплавленный материал, поскольку окисляет его путем создания оксидного слоя.
Химические свойства кислорода позволяют с его помощью сделать более быстрый разрез. Особенно часто он применяется для резки материалов, толщина которых начинается от 25 мм. Подобным образом с его помощью создают различные металлоконструкции в судостроении, при производстве оборудования, предназначенного для заводов, фабрик.
Преимущества кислорода:
- Более быстрая резка. Примерно на 30%, чем у азота.
- Дополнительное тепло. Благодаря ему получается справиться с материалами, толщина которых превышает стандартную.
- Небольшой расход. Следовательно, расходы на производство тоже снижаются.
К сожалению, у этого вспомогательного газа все же есть свои недостатки. Среди них:
- Влияние на последующий процессы. Поскольку у некоторых сталей он может вызывать упрочнение кромок, то с варкой или формовкой могут быть проблемы.
- Окисление. Из-за него нельзя использовать кислород в процессе резки стальных или алюминиевых деталей, поскольку свойства материала могут ухудшиться, начнется процесс коррозии.
- Грубая режущая кромка. Она возникает из-за реакции окисления. После получения грубой кромки понадобится дополнительная обработка материала.
Все эти нюансы обязательно нужно учитывать при выборе.
Азот
Инертный газ, применение которого обеспечивает высокое качество реза, не приводит к окислению материала. Азот также охлаждает режущую кромку, благодаря чему зона термического воздействия становится минимальной.
Азот часто используется для резки нержавеющей стали, а также цветных металлов, которые не должны подвергаться окислению.
Преимущества азота:
- Максимально чистый срез. Благодаря ему материал в дальнейшем не нужно будет обрабатывать.
- Отсутствие окисления. Азот отлично справляется с резкой цветных материалов и тех, что обладают высокой светоотражающей способностью.
- Сохранение свойств материала на режущей кромке.
К недостаткам этого газа можно отнести:
- Потребность в высоком давлении. Азоту требуется не менее 10-25 бар, чтобы можно было нормально разрезать материал. Это может привести к более высоким расходам, требованиям к используемому оборудованию.
- Более низкая скорость резки, если сравнивать резку с применением кислорода. Если толщина материала составляет более 3 мм, то процесс будет длиться дольше.
Если планируется использовать азот, то нужно быть готовыми к тому, что придется потратить больше средств на источник лазерного излучения, системы, генерирующие высокое давление. Зато благодаря отсутствию выделения тепла последующая обработка обойдется дешевле.
Давление и средний расход газа
Для кислорода требуется давление от 0,5 до 6 бар. Оно напрямую зависит от толщины материала, который подвергается резке. Средним показателем считается интервал от 2 до 5 бар. Средний расход составляет примерно 5 Нм³/час.
Для азота требуется давление от 10 до 20 бар. Иногда и этого давления может не хватать, поэтому показатель увеличивают до 30 бар. Средний расход составляет примерно 50 Нм³/час.
Чистота газа и его свойства
Для резки лазером используют только чистый азот (99,999%), а также стандартный (99,5%) или чистый (99,95%) кислород.
Чистый азот
Он обеспечивает:
- отличную защиту от окисления;
- отсутствие лишних химических реакций.
Если в азоте содержатся примеси воды, то режущие кромки могут окислиться, а если кислород, то чувствительные материалы начнут обесцвечиваться. Наиболее опасны примеси углерода, ведь они вызывают снижение мощности лазера и даже могут повредить оптику.
Чистый кислород
Стандартный кислород применяется для обычных процедур. Им обычно режут мягкую сталь, толщина которой не превышает 10 мм. Кислород высокой чистоты используют там, где требуется разрезать толстую сталь и при необходимости получить кромки высшего качества.
Примеси в кислороде, используемом для лазерной резки, могут оказать катастрофическое влияние на качество обработки материала, например, привести к изменению свойств лазерного луча. Кроме того, примеси могут вызвать образование оксидов на краях реза. Это не только ухудшает внешний вид обработанной детали, но и искажает ее механические свойства.
Где можно хранить газ
Для хранения газа могут использоваться:
- баллоны и стеллажи;
- резервуары;
- мини-танки.
Баллоны из легких сплавов или стали предназначены для хранения сжатого газа под высоким давлением. Их можно устанавливать в различных местах, начиная от производственных цехов и заканчивая лабораториями.
Стеллажи позволяют организовать компактное и безопасное хранение нескольких баллонов, обеспечив при этом доступность и контроль за состоянием газов.
К преимуществам баллонов и стеллажей можно отнести: легкую реализацию, универсальность, мобильность. Среди минусов — необходимость частой замены, ограниченность емкости, более высокая цена за одну единицу объема, много требований к транспортировке.
Резервуары больше предназначены для промышленных нужд. Обычно эти места хранения представляют собой большие емкости, способные сохранять газ в жидком состоянии при низкой температуре или под давлением. Резервуары обеспечивают надежное хранение и минимизируют риск утечек, что особенно важно для вредных или горючих газов. Они могут быть как наземными, так и подземными. Правда, для конверсии газа нужно будет приобретать дополнительное оборудование.
Мини-танки позволяют грамотно распределять запасы. Они быстро устанавливаются и повышают уровень безопасности на рабочем месте.
Для более качественной лазерной резки нужно правильно подобрать вспомогательный газ, а также выбрать место, где он будет храниться. Необдуманное решение часто приводит к внезапным затратам, порче оборудования, снижению уровня безопасности на производстве и т.д.
Поделиться в соц. сетях: